DRILLING PROCESS
Working of Drilling Machine: Drilling is a material removal operation. The
component is clamped securely on the work table and the cutting tool i.e. Drill rotates at a
cutting speed and is feed into the job. The material removal takes place in the form of chips.
Selection of Drill nomenclature i.e. Point angle , Helix angle and no of
cutting flutes depends upto the material to be drilled. The Cutting Angle (Point angle ) can be
modified whereas the latter are fixed by Drill manufacturers. For Drilling: Ferrous metals the
point angle is kept as 118°, Non Ferrous Metals @ 140° and for Plastics
< 80°.
Cutting speed depends upon the material to be Drilled, type of drill used, rate
of Feed and depth of hole. For Drilling Ferrous Metals cutting speed reduces with the increase
in tensile strength (5-8 m/min for tool steels & 20-23 m/min for mild steels). Non Ferrous
Metals @ 35-105 m/min.
Feed depends upon cutting speed and drill diameter. It increases with the
diameter of drill (Drill Ø 1.5mm feed @ 0.04 mm/rev, for Drill Ø 38mm & above feed @ 0.4 mm/rev)
SELECTION OF DRILLING MACHINES
Selection of Drilling Machine or Drill Press depends upon the Material to be Drilled. The material’s can be classified into three major categories namely: Ferrous Metals, Non Ferrous Metals & Plastics. The most important material property to refer is its ultimate Tensile Strength. Vertical Drill Machines are rated/designated by their max drilling capacity in mild steel (60 Kgf/mm2). A good quality drill machine should have a sturdy construction, fitted with high quality Bearings, Quality cast head with an accurately honned quill bore (true to machining table), balanced pulleys with least vibrations. Spindle and Quill assembly to be concentric so that holes drilled are precise and of high accuracy. Drilling Machine cost should be viable guaranteeing a long and trouble free life.
MACHINE CONSTRUCTIONAL PARAMETERS
Spindle nose to table | Maximum height of component which can be held. |
---|---|
Throat depth | Maximum distance from the edge of component to the twist drill centre line. |
Spindle nose to base | Used for large or heavy components. |
Column Dia/Length | Should be sufficient to maintain rigidity. |
Spindle travel (stroke) | Determines maximum depth of hole. |
Spindle Speeds | Should be sufficient to offer wide speed range. |
Drilling capacity | Sizes of Hole to be drilled. |
The above specifications varies from different Drilling Machine Manufacturers and needs to be examined before buying Drilling Machine. Often the drilling operation and spindle speeds are precisely associated. The range of spindle speeds determine minimum / maximum size of Drill that can be successfully performed on a machine. Drill Dia and spindle speeds are inversely associated i.e. larger drill requires low speed and smaller drill requires high spindle speed. Drill Machine with a multiple speed range is recommended.
SELECTION OF DRILLING MACHINES
Selection of Drilling Machine or Drill Press depends upon the Material to be Drilled. The material’s can be classified into three major categories namely: Ferrous Metals, Non Ferrous Metals & Plastics. The most important material property to refer is its ultimate Tensile Strength. Vertical Drill Machines are rated/designated by their max drilling capacity in mild steel (60 Kgf/mm2). A good quality drill machine should have a sturdy construction, fitted with high quality Bearings, Quality cast head with an accurately honned quill bore (true to machining table), balanced pulleys with least vibrations. Spindle and Quill assembly to be concentric so that holes drilled are precise and of high accuracy. Drilling Machine cost should be viable guaranteeing a long and trouble free life.
MACHINE CONSTRUCTIONAL PARAMETERS
Spindle nose to table | Maximum height of component which can be held. |
---|---|
Throat depth | Maximum distance from the edge of component to the twist drill centre line. |
Spindle nose to base | Used for large or heavy components. |
Column Dia/Length | Should be sufficient to maintain rigidity. |
Spindle travel (stroke) | Determines maximum depth of hole. |
Spindle Speeds | Should be sufficient to offer wide speed range. |
Drilling capacity | Sizes of Hole to be drilled. |
The above specifications varies from different Drilling Machine Manufacturers and needs to be examined before buying Drilling Machine. Often the drilling operation and spindle speeds are precisely associated. The range of spindle speeds determine minimum / maximum size of Drill that can be successfully performed on a machine. Drill Dia and spindle speeds are inversely associated i.e. larger drill requires low speed and smaller drill requires high spindle speed. Drill Machine with a multiple speed range is recommended.
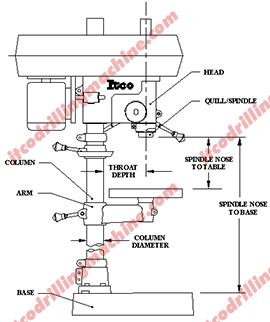
SALIENT FEATURES OF ITCO MACHINES
- Designed and built with an expertise of more than five decades in machine tools.
- Sturdy streamlined construction enables to withstand & absorb heavy cutting forces.
- High grade alloy steel carburized, case hardened & precision ground to close tolerances used for main drive elements i.e. spindle, quill, sleeve, gears etc.
- Drill head, arm & other casting parts made from graded casting for high rigidity.
- Spindle Hardened & Ground with internal taper ground.
- Spindle Runout at final testing within 10-20 microns.
- Column made of seamless steel tube precision ground & hard chromed.
- Main gears, spindle & motor pulleys are perfectly balanced to avoid vibrations.
- Wide range of spindle speeds & feeds to facilitate operations of Drilling Machine: Drilling, Tapping, Reaming, Spot facing, Counter Drilling, Boring etc.
- Accurately bored & Honned quill bore is square to work table.
- Working table provided with Machined T-Slots & Clamping system.
- Table Runout (right angle) 30 to 40 microns.
- Total Interchangeability of parts.
- All moving parts accurately machined & ground to close tolerance.
- Accuracy of Drilling Machine confirms as per IS-2425.
- Accuracy of Tapping Machine confirms as per IS-6175.
- Dealership network at all the major cities in India.
- Excellent after sales service.
- 2 years Warranty.
Copyright © Itco Drilling Machine Jalandhar, Punjab (India)